Food Safety Focus | Product Hold
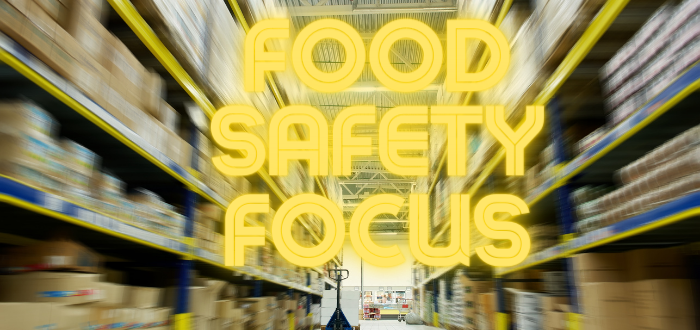
Hello All!
I hope this message finds all of you and your families safe and well.
Last week we discussed recalls and the importance of good labeling. This week I want to talk a little about product hold so we can trace a product for a recall if needed.
To accurately track or trace a product, you will first need to put a product on “hold” to stop the product from moving physically or in the system while you track it. You don’t want orders being pulled and shipped with the product you are trying to find. You may need to clear off any pending orders that include the product you are tracing to have the ability to put the product on hold, if needed. You will not be able to put the entire product on hold until you remove the entire product from pending orders.
Next, remove the product physically from all orders still in-house, including sitting on the dock or on a trailer still at the site and from off the pickline. Move all inventory to a safe place that will not be touched, to get it ready to be counted for the trace part of the recall. Hold areas that are designated in the warehouse can be temporarily expanded if needed. Put hold signs on the product you are tracing to ensure it doesn’t accidently get used while you track it for the trace part of the recall.
Remember to keep everything in writing, including management or customer requests to have product placed on hold or to have product taken off hold.
We’ll talk more about recalls again next week.
Thanks for all that you do every day!
Justin
Food Safety Manager
- Food Safety Focus | Fruitcake
- Food Safety Focus | Food Safety
- Food Safety Focus | Focus on Cotton Candy
- Food Safety Focus | Focus on Trailer Inspections
- Food Safety Focus | Cinnamon
- Food Safety Focus | The Winds of Stress
- Food Safety Focus | National Taco Day
- Food Safety Focus | MHE Safety
- Food Safety Focus | Peanut History
- Food Safety Focus | Pre-Cooled is the Coolest Way to Be
- Food Safety Focus | Marshmallows
- Food Safety Focus | Sanitation
- Food Safety Focus | Wrap It Up Clean
- Food Safety Focus | Focus On Popsicles
- Food Safety Focus | National Hotdog Day
- Food Safety Focus | Apple Turnover Day
- Food Safety Focus | Safety Culture
- Food Safety Focus | National Cucumber Day
- Food Safety Focus | Pet Food Safety
- Food Safety Focus | Asparagus
- Food Safety Focus | Happy Walnut Day!
- Food Safety Focus | Talkin’ Trash
- Food Safety Focus | Hazard Analysis
- Food Safety Focus | Trailer Inspections
- Food Safety Focus | A Place for Everything
- Food Safety Focus | The Right Temperature
- Food Safety Focus | Don’t Stress
- Food Safety Focus | Seals
- Food Safety Focus | I Love It When A Plan Comes Together!
- Food Safety Focus | Baby Formula News
- Food Safety Focus | Space Food
- Food Safety Focus | I Love It When A Plan Comes Together!
- Food Safety Focus | Focus On Taking Time Off
- Food Safety Focus | No Added Flavor Needed
- Food Safety Focus | Focus
- Food Safety EXTRA | The Turkey Prince
- Food Safety Focus | Doors & History
- Food Safety Focus | Keep Common Sense Common
- Food Safety Focus | Gourmet Coffee Legend and History
- Food Safety Focus | EMA
- Food Safety Focus | New Allergen – Sesame
- Food Safety Focus | Food Poisoning
- Food Safety Focus | Cell Based Meat
- Food Safety Focus | No Waste is a Tasty Idea!
- Food Safety Focus | Floors
- Food Safety Focus | Hand Washing Culture
- Food Safety Focus | Falling Cases
- Food Safety Focus | Turkey Myths
- Food Safety Focus | Root Cause Analysis
- Food Safety Focus | Chemicals
- Food Safety Focus | Focus on Drips
- Food Safety Focus | Freezer Gear Housekeeping
- Food Safety Focus | Eat and Drink in the Right Place
- Food Safety Focus | Food Safety During the Storm
- Food Safety Focus | High Quality H20
- Food Safety Focus | Who is Responsible for Food Safety?
- Food Safety Focus | Baby Food & Avoiding Toxic Metals
- Food Safety Focus | MHE Impact
- Food Safety Focus | Kill Step
- Food Safety Focus | MHE Inspections
- Food Safety Focus | Product Weight Limits
- Food Safety Focus | Awareness Part 2
- Food Safety Focus | Awareness Part 1
- Food Safety Focus | FDA Reported Listeria Outbreak
- Food Safety Focus | Listeria
- Food Safety Focus | Hot Dogs
- Food Safety Focus | Recall Classes
- Food Safety Focus | Mock Recall – Getting Started
- Food Safety Focus | Don’t Cause a Recall
- Food Safety Focus | Product Hold
- Food Safety Focus | Labels and Recalls
- Food Safety Focus | Allergen Update – Sesame Seeds
- Food Safety Focus | Ceilings
- Food Safety Focus | Floors
- Food Safety Focus | Damage Control
- Food Safety Focus | Pest Control
- Food Safety Focus | Dumpster Duty
- Food Safety Focus | Standing Water
- Food Safety Focus | Wrap Care
- Food Safety Focus | Foreign Matter
- Food Safety Focus | See Something, Say Something
- Food Safety Focus | Pallet Identification
- Food Safety Focus | Tunnel Vision
- Food Safety Focus | Super Bowl Safety
- Food Safety Focus | Receiving Temps
- Food Safety Focus | Food Safety Attitude
- Food Safety Focus | MHE
- Food Safety Focus | Pallets, Racks & Racking
- Food Safety Focus | Security
- Food Safety Focus | Hand Washing Importance
- Food Safety Focus | Holiday Food Safety
- Food Safety Focus | Accurate Record Keeping
- Food Safety Focus | Importance of Training
- Food Safety Focus | Thermometer Checks
- Food Safety Focus | Allergen Storage
- Food Safety Focus | Pest Control
- Food Safety Focus | PPE
- Food Safety Focus | Food Safety Culture